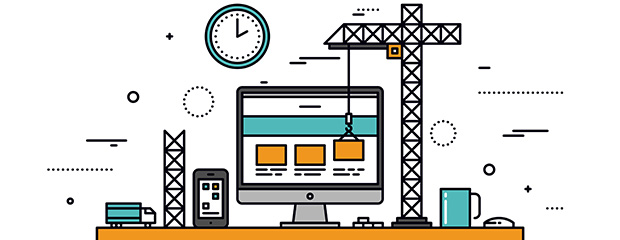
Let’s start off with a brief look at what BIM is. The purpose of BIM is to give each actor just the information they need at just the right time throughout a building’s lifecycle to support its effective design, creation, and use.
- The “B” in BIM stands for “Building” – since it’s about methods and technologies for the effective design, creation, and use of buildings.
- The “I” in BIM stands for “Information” – the 3D representations and non-graphical data in the digital model of a building. It’s the key to managing a building throughout its lifecycle.
- Besides 3D information – for design, engineering, and production – there’s also
- 4D information that incorporates time (scheduling, planning, and control),
- 5D which adds costs and analysis,
- 6D that includes sustainability, and
- 7D which looks at facility management over the entire lifetime of an asset.
- Besides 3D information – for design, engineering, and production – there’s also
- The “M” in BIM has three meanings:
- “Modelling” – the collaborative processes by which actors create, update, and store relevant information about a building throughout its life.
- “Model” – the ‘data container’ or digital model of a building where information about the building is stored.
- “Management” – actors’ use of a building information model for their needs.
Libraries in BIM
Currently there are plenty of software options available, any one of which can be selected as a BIM environment for design. Most of them use generic libraries that favor the development region or country’s standards (Revit and US standards, DDS-CAD and German standards, etc.). To design a real building, we need real-world elements with real behavior.
So, engineers’ needs and software content usually veer off in two different directions.

What engineers need | What software provides | Engineer’s exact needs |
Ducts | Generic ducts | Branded ducts |
Duct fittings | Generic duct fittings | Branded ducts |
Air terminals | Generic air terminals | Branded air terminals |
Duct accessories | Generic duct accessories | Branded duct accessories |
Mechanical equipment | Generic mechanical equipment | Branded mechanical equipment |
As a software developer, I understand that adopting an element to the needs of every country is a dauntingly difficult task for global software companies, but we have to find a solution for that! And – get this – the solution should come from manufacturers.
Yep. Manufacturers.
Why manufacturers?
- Errors — There’s a greater possibility of human error when content is created “on my own”.
- Business — Every element used in a BIM model should be purchased and installed in the building – thus arises a good business opportunity for manufacturers. Elements can be connected to the manufacturer’s data (e.g. price, where to buy, URL, etc.)
- Product changes — Manufacturers – and only manufacturers – know all production changes and can easily fix and publish content.
- Software changes — Manufacturers can keep track of software changes and update the objects immediately.
Good examples of good BIM content
A good example of good BIM content is not one that is created, published, and forgotten. That would be a good example of bad BIM content.
A good example of good BIM content is when an element is created logically. Good BIM content has all the needed parameters – but not too many (after all, we’re not going to manufacture this element, so why do we need extra information about it?). Good BIM content has enough LOD to understand it – but is not too detailed. Good BIM content has 2D representation. Good BIM content sometimes even has some limitations placed on the end user. Really good BIM content should be always up-to-date. It should be revised after every main software release, and if failures are found it should be fixed immediately. Bottom line: To prevent BIM content from the fate of being published and forgotten about, manufacturers should take care of their content!
There are lots of manufacturers on the market that provide BIM content in one way or another. One example is SALDA VentMaster.
- It has a live connection with AHU selection software
- All needed parameters are transferred from Revit project to selection software and back.
- It updates the family if changes are found in the design.
- It’s free.
What I like are innovative approaches to customers through apps or configured libraries because it means I can start my work NOW, without extra setup.
Why apps and not just families?
I think this could be a great benefit for manufacturers. By using apps, manufacturers can gather needed data from the customer – and tap straight into the whole purpose of BIM, of supplying just the right information at just the right time.
Here are some things that apps can give manufacturers insight into.
- Where customers are based. Manufacturers can input different sales data into the families or differentiate their families by units (metric or imperial).
- What kind of elements a customer is grabbing from their library (statistics).
- How often users are using their content (statistics).
And here are two other examples of app advantages.
- Manufacturers can instantly update their content on the user’s computer. Usually customers download content and use that for the rest of the job. And…what if manufacturer decides to stop production of this or that brand or change some main parameters of the object…? Bingo. Instant updates.
- Since an app is connected with the manufacturer’s data, users can get prices instantly and use that in cost estimates. This would be really beneficial for both the manufacturer and designer.
Don’t overpay for your content
Designers have certain needs that manufacturers should know about. Now hear this, manufacturers: your BIM objects will be used NOT for fabrication but for design, so do not overload your elements with unnecessary detail. You will pay $$$ for this task, but nobody needs unnecessary details. (I know that’s redundant, but it needs to be said.) All the details are only used in manufacturing, but, as mentioned before, designers do NOT manufacture: they DESIGN.
What engineers don’t need.

What do engineers need? We need only main data. Don’t forget, we designers do NOT manufacture: we designers DESIGN.

Again, we designers need only main data. Say it with me now! Designers do NOT manufacture: designers DESIGN.
Engineers need:

And what do manufacturers need? Don’t forget about yourselves, manufacturers. You have to put your identity info out there as well as data that will help you sell the product. In my opinion, this could be things like product serial number, price, or unique product code that correspond to your inner data management system. I could continue rattling off a list: manufacturer data, model, company URL, product URL, product documentation, where to buy, phone number…you get the gist.
How to increase sales?
- Rely on really advanced element creators.
- Don’t overload your BIM objects.
- Don’t forget about yourself.
- Make registration mandatory to download files.
- Use a tool to track your customers (Cloud solution).
- Use a tool to communicate with your customers.
- Make BIM content free or at least reasonably priced.
- Content should be easy to use or at least easy to start.
- Create apps – they’re more efficient!
Additional material
I actually gave a seminar on this very topic of BIM content for the Eurovent Association, so here you can see my presentation on AGACAD’s YouTube channel.